Management approach to EV development
Strategy formulation
Yulon Motor maintains its market competitiveness in the automotive industry with the new product R&D strategy oriented on the following 5 aspects:
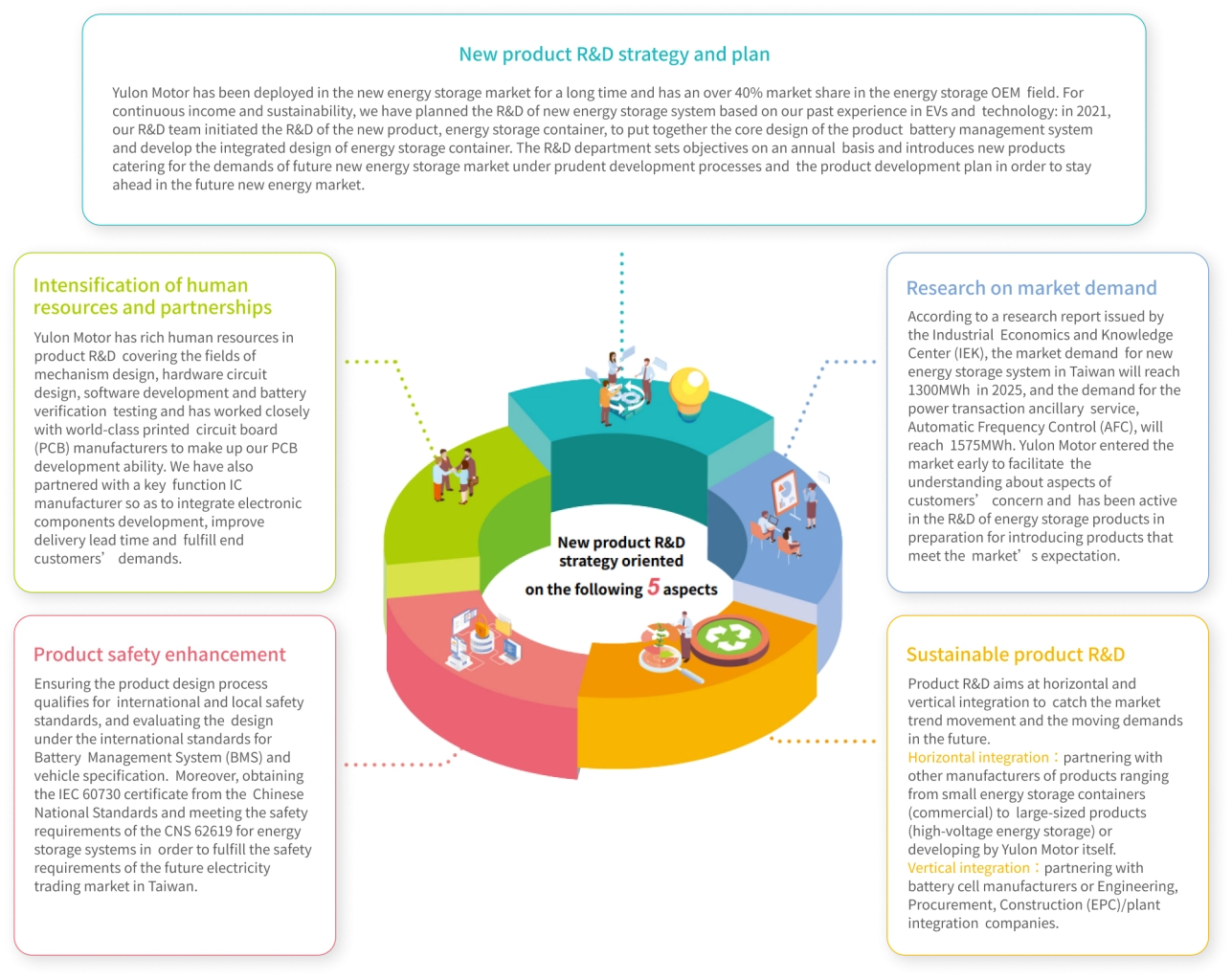
Goals
Yulon Motor has set the short-, mid- and long-term goals in various R&D categories and regularly reviewed and tracked the development progresses:
Innovation and R&D results
Yulon Motor’s innovation and R&D results of 2022 are classified into six categories:
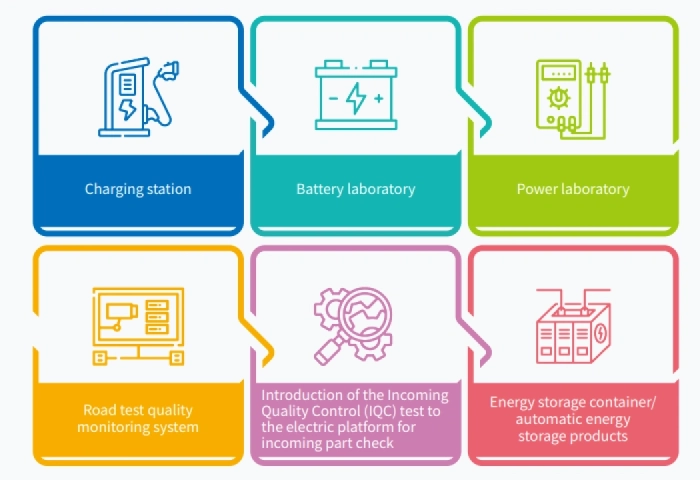
-
1.Charging station
Yulon Motor’s professional system design, development and operation teams have built a complete charging service operation system, which features the advantageous ability in customization and connection with external systems and can address the needs of both EV owners and charging sites. In 2022, we operated 206 vehicle charging stations and 109 motorcycle charging stations in total, and the charging counts have reached over 300,000 times.
-
2.Battery laboratory
We established an ISO 17025-Quality-System-certified battery laboratory that provides professional battery testing technology consulting and planning and other thorough peripheral services as well as grid search, best match and customization services for customers’ battery products. In 2022, the laboratory tested 3 items including the battery cell, module and battery pack:
- Battery cell: completed the longevity test for 4 energy-storage battery cells and the performance and thermal model test for 2 energy-storage battery cells
- Module: completed the longevity test for 1 battery module for forklifts and energy storage
- Battery pack: completed the capacity test for 2 energy storage containers and the capacity and longevity test for 2 power batteries
-
3.Power laboratory
A power laboratory with an ISO 17025 Quality System certificate and the world-class automatic vehicle location (AVL) system was also established. This laboratory has the experience in the developing tests for EV driving motors and powertrains and the inspections for compliance, and with the achievement in the simulation of energy consumption under working conditions, in which tests were carried out under multiple edit modes similar to actual driving conditions, enabled early prediction of product issues and effective improvement and confirmation before mass production. In 2022, we completed the performance test for 7 motors (scooter, all-terrain vehicle, logistics vehicle, passenger car, electric bus, electric yacht) and the rolling resistance and minimum energy performance tests for 3 vehicles (Luxgen Model C, Volkswagen ID4, Hyundai IONIQ 5).
Photo of the power laboratory
-
4.Road test quality monitoring system
Yulon Motor has improved the road test quality test by transitioning from the determination by human senses to the determination by vehicle signals. With sufficient quantity of data, such determination is now made by the system, which immediately imports data to create a resume and further improve the test quality. A total of 30,439 vehicles were tested in 2022 with a 100% test quality assurance rate on finished vehicles, and we did not receive any significant customer complaint in 2022.
-
5.Introduction of IQC test to the electric platform for incoming part check
Developed three-wheel logistics vehicle incoming part check electric platform, which mainly uses analog signal in part durability tests and detects abnormal parts in early stages to eliminate the waste of time for re-installation if any abnormal parts enter the production lines. In 2022, the platform tested 1,640 pieces in total, covering 41 types of part and 40 models of vehicle, and detected 3 abnormal lenses and 2 abnormal push buttons. The test completion rate and the part pass rate were 100% and 99.7%, respectively.
-
6.Energy storage container/automatic energy storage products
We provide measurement, assembly and testing services for parts used by customers to build complete battery cells, modules, battery packs, controllers, junction boxes or energy storage containers, and testing services such as environmental temperature humidity performance test for high-power energy storage system and large power battery charging and discharging test. In 2022, we assisted eight clients in the development of laser welding technology for their products such as energy storage products, automotive batteries, and traditional mechanical parts, and the application of a wide range of materials. In addition, in 2022, we also completed one set of prototypes of 250KW energy storage racks, had the functional safety standards for BMS verified for our compliance with the ISO 13849-1 PLC Standards, which effectively mitigate the risk of product malfunction, and the IEC60730 international safety standard, and completed 2 patent applications.
Yulon Motor’s energy storage products – a pioneer of green energy business
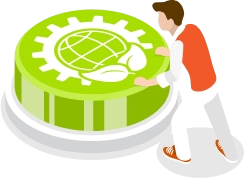
Yulon Motor’s energy storage products feature:
-
1Premium product assembly capability
-
2Digital management system with 100% energy storage coverage rate and penetration rate.
-
3High capacity for development and procurement. We work with 98 energy storage part and equipment manufacturers and Chinese battery cell suppliers to help clients develop their parts.
-
4Global logistics and coordination capability. It uses the SCM supplier management system to control a total of 322 domestic and overseas suppliers and 17,900 types of part.
Furthermore, we has the ability for developing industrial energy storage cabinets and battery management systems and the ability for measuring and testing new batter y management system and batteries, ahead of many firsttier world-class manufacturers. Yulon Motor’s existing production lines can produce energy storage containers of a maximum capacity of 1.6GWh per year. We are so competitive in the market that when the existing production lines are overloaded, we can expand with an additional maximum capacity of 1.02GWh per year within a 6-month period. Due to the China-US trade war in recent years, the US clients have been active in seeking overseas contracting manufacturers outside China. Since Yulon Motor owns the top laser welding technology for manufacturing EV batteries, we have earned clients’ trust with our technology and rich experience. Until now, we have manufactured energy storage containers with a total capacity of 200MW and won ourselves the title of best assistant in sustainability and carbon reduction with its leading green energy technology.
Yulon Motor has launched the project to trial run the production of the private brand EVs and prepare for mass production. A production plan tailored to EV products and the characteristics of EV parts and combined with our experience in fossil fuel vehicles manufacturing on the three major aspects is prepared and described as follows:
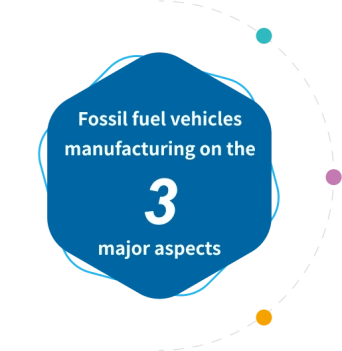
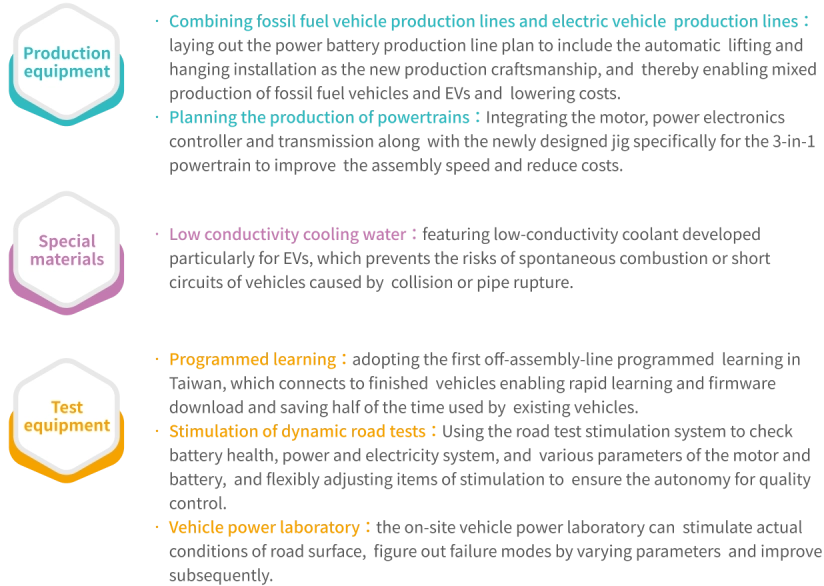
Main production process of EVs
-
Assembly and installation
The production technology unit first lays out the power battery production line plan covering automatic lifting and hanging installation, jigs and tools for installation, procedures and order of installation and foolproof mechanism plan to achieve the mixed production of fossil fuel vehicles and EVs.
-
Material delivery
The supply unit is responsible for planning the shelve for materials and position thereof, the picking and allocation methods and the foolproof mechanism, and by considering the weight, size and safety of EV batteries, laying out the storage location and transportation route.
-
Part and vehicle inspection
The quality inspection unit inspects incoming materials and verifies specifications, and the electronic inspection platform inspects vehicles under conditions including static and dynamic conditions, pouring rain, on road at night and exposure to sun. We have adopted the first offline programmed learning system in Taiwan and use the road test stimulation system to check battery health, power system and the parameters of electronic battery. The items for stimulated tests may be adjusted flexibly to ensure the autonomy for quality control.