Risk assessment and identification
Yulon Motor has adopted the“ Procedures for Hazard Identification and Risk Assessment” and requires the personnel in charge of each unit to participate in the risk assessment personnel training and to take responsibility for facilitating risk assessments, assisting in the hazard identification, risk assessment and control measures of new operations or changes to operations, updating information and proposing proper strategy based on the assessment results. When introducing new equipment, a public hearing shall be held at the plant, and a joint evaluation by biotechnologists, the environmental safety department and the safety and health department shall be conducted to make sure the specifications of equipment comply with laws and the installation processes thereof meet the safe operation standards. Procedures for identifying hazards to occupational safety and health and determining risks and opportunities:
Procedures for Hazard Identification and Risk Assessment
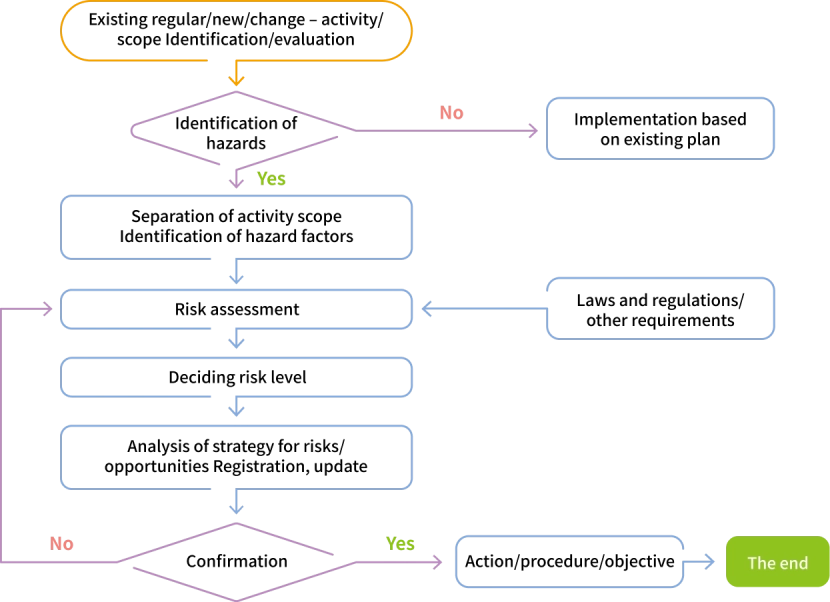
Procedures for handling occupational accidents
Yulon Motor has adopted various environmental safety corrective measures and programs. In situations such as unexpected condition, false alarm, events that may cause accidents, occupational diseases, financial losses, plant damages, losses in production or legal liabilities, the corrective programs will be activated. Moreover, Yulon Motor has enacted the Procedures for Handling and Investigating Accidents, and the emergency handling and subsequent investigation of accidents happened to employees or contractors are made accordingly followed by a review of risks in connection to occupational disasters to mitigate losses arising from accidents and prevent similar accidents from happening. Additional resources from various sources are also provided to educate employees about safety and enhance their safety awareness.

Data of occupational accidents in 2022
Note:
- 1. The absence rate was calculated based on the absence of employees losing work ability, not limited to the reason of an occupational injury or disease, which may include occupational injury leave, sick leave, menstrual leave and personal leave.
- 2. The number of workdays lost was calculated based on the“ number of days lost” in which workers are incapable of handling daily job as a result of an occupational accident or disease.
- 3. The number of persons involved in series occupational injuries excluded the number of deaths.
- 4. Total number of occupational injuries = number of persons injured + number of deaths.
- 5. Total work hours = total number of working employees × number of work hours per day × number of actual workdays in the year.
- 6. Occupational injury rate = total number of occupational injuries/Total number of work hours×200,000.
- 7. Absence rate = total number of absence days / total number of work person-days × 100%.
- 8. Rate of workdays lost = number of workdays lost as a result of occupational injuries / expected total work hours of the worker (total number of work hours) × 200,000.
- 9. All rates were rounded to 3 decimal places.
Occupational disease prevention and management
Pursuant to the Occupational Safety and Health Act, we engage the service of a job site monitoring and testing agency approved by the Ministry of Labor to conduct one job site monitoring and testing semiannually where the monitoring plan is formulated in an evaluation team’s meeting at the plant and attested by an industrial and mine safety and health engineer. The monitoring and testing on a total of 333 items were conducted in April and October of 2022, and the results were announced at each job site and unit. The monitoring has concluded that the levels of organic solvents, specified chemical substances, extremely exuding dust and carbon dioxide concentration of the central air-conditioner all met the legal standards, except that noise at some workstations has exceeded the limit and corrective measures have been implemented. The said measures included posting the noise warning sign at obvious space and the reminder for wearing hearing protection gears, checking if employees wear hearing protection gears from time to time, carrying out special health check for groups exposed to noise and implementing hearing protection plan. The professional occupational disease doctors and nurses also evaluate if it is necessary for an employee to switch workstations on-site, and if yes, the safety and health office and human resources team consequently coordinate the relocation of such an employee. There were not diseases or deaths as a result of occupational diseases in 2022.
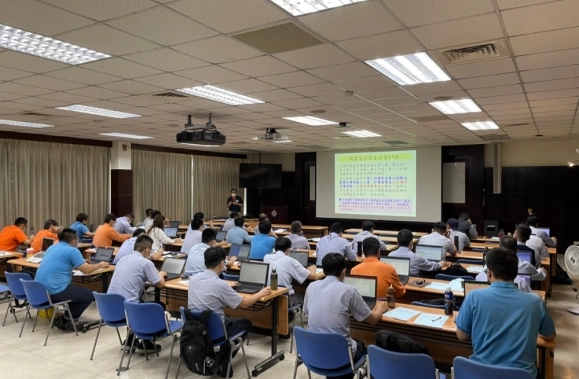
Education and training on occupational safety
In addition to the management of equipment, the dissemination of occupation safety also play a key role in the occupational accident prevention plan. We hold regular education and training on occupational safety covering foreknowledge of hazards and safe operations, safety management approach case study, a series of courses on building inherently safe design of machineries, hazard prevention, basic and advanced principles of risk management, theory and practice of firefighting and rescue, training and regular drills for members of the Emergency Response Team (ERT), transportation safety workshop, education and training on hazardous machinery and equipment, safety and health education training for contractors, etc. The training time totaled 2,324 hours in 2022.
Since the second half of 2022, we have invited the retired team leader of the Occupational Safety Center to customize a series of courses in connection to labor inspection laws and practice to enhance supervisors and employees’ awareness of the Occupational Safety and Health Act, the keys to labor inspection, the regulations concerning high-risk operation and the concept of contract management by capitalizing the rich experience of the instructors. These courses include:
-
LESSON1
Case study of construction hazards (focusing on remodeling at the plant, equipment installation, prevention of electrification and falling, etc.)
-
LESSON2
Work safety analysis of the current work safety plan, and to teach concerned employees about the essentials of such operation
-
LESSON3
Review of processes/forms related to labor inspection and practice
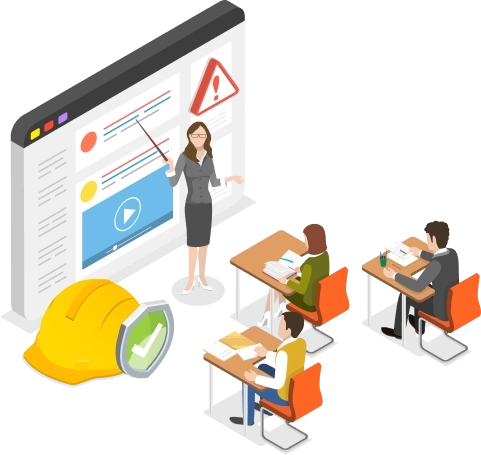
Employee healthcare
We enroll all employees not only in the labor insurance and health insurance lawfully but also the group insurance, which covers the employees and their spouses and children, and is paid by the Company. To take care of the employees and their health, the Company also establishes an“ employee clinic” providing medical, surgical, smoking cessation services and various medical education and consultation services for the employees. We also care about employees’ mental health, so we organize the seminars for emotional management, stress relief, disease prevention and healthcare from time to time and take care of employees’ family by hosting seminars for family, parents and children to provide employees complete health management covering every member of their family, who is also a family of Yulon Motor.
2022 Health Promotion Plan
Hazard prevention Healthcare
Name of major plan/activity
- Providing general and specialized operation health check for incumbent employees, implementing health rating management and conducting an analysis on the health checkup data.
- 4 major labor health protection plans
Performance in 2022
- A total of 281 employees had a health check-up in 2022
- The general health check-up is offered once every 3 years, better than that is required by laws, and the specialized operation health check-up is provided every year.
- Providing advanced health check-up at contracted hospitals to senior executives every year
- Adopting the health management rating standard table and distributing health education leaflets and offering proper health education information to employees based on the rating
- 3 doctor on-site services every month
- Appointing professional occupational medicine doctors to provide one on-site health service every month (3 hours/time)
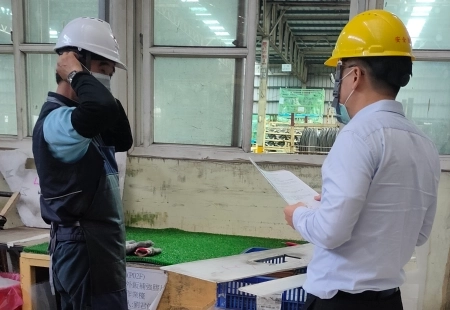
On-site visit of the occupational medicine doctors
Hazard prevention Healthcare
Name of major plan/activity
- Establishing the Yulon Motor Employee Clinic
Performance in 2022
- Formed by one specialist in family and emergency medicine and two full-time nurses. Employees can see the doctor, seek health advice, or take emergency treatment during the work time.
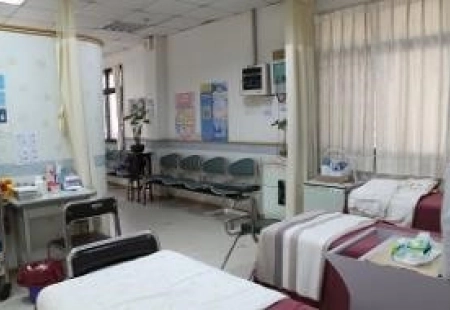
Employee Clinic
Emergency rescue training course
Name of major plan/activity
- Cardio-Pulmonary-Cerebral-Resuscitation (CPCR) training and installation of AED
Performance in 2022
- There are 8 Shinkong Communication AEDs installed at Yulon’s Sanyi plant, which are maintained semiannually to ensure normal functioning as well as safety.
- In 2022, we organized 1 online CPCR course and 3 physical CPCR courses in total, and each had 50-120 participants.
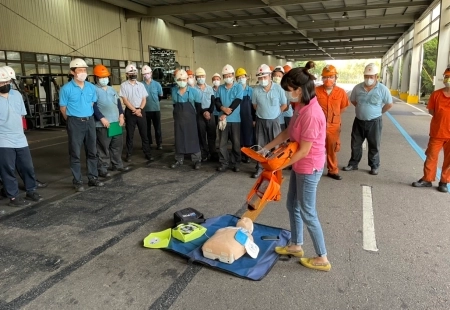
CPCR instruction
Safe breastfeeding environment for mothers at workplace
Name of major plan/activity
- Setting up a breastfeeding room
Performance in 2022
- We provide free supplies in the breastfeeding room and create an exclusive private and safe space for breastfeeding mothers allowing secured breastfeeding and collecting after they reinstate in work. There were two mothers using the breastfeeding room in 2022.
Name of major plan/activity
- Parents’ sharing session
Performance in 2022
- We held a blindfolded diaper change game on 2022/11/25 together with the practical“ Baby First Aid Seminar” and the“ DIY Towel Bear Activity,” and 50 persons in total participated in these events.
- Hosting parenting activities in which the“ Mother’s Gift” is distributed at the infirmary
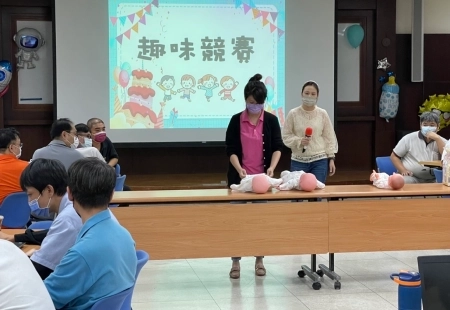
Mothers and babies’ sharing session
Health promotion activities
Name of major plan/activity
- Joint dissemination of health at the infirmary and via the Line APP
Performance in 2022
- A total of 53 sharing sessions for health promotion were held in 2022
Name of major plan/activity
- Eligible employees apply the government-funded influenza vaccination at the Employee Clinic.
Performance in 2022
- In 2022, the Employee Clinic applied to become a medical care institution eligible for providing the government-funded influenza vaccination and vaccinated 120 persons in total.
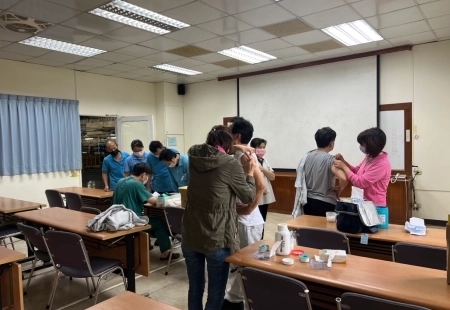
Vaccination in 2022