Management approach to product quality and reliability
Product quality and safety are critical to Yulon Motor, so we observe the most rigorous standards and procedures in the production process:
Systems and certifications observed by Yulon Motor
-
ISO 9001
Quality management system
-
IATF 16949
Quality management system verification
-
ISO 14001
Environmental management system certification
-
ISO 17025
Quality system certification
Product quality management
Yulon Motor has developed the production process management systems to ensure stable quality and at the same time build up a production resume for vehicles covering important part information, offline service record, quality resume, etc., as a reference for future repair and maintenance. In 2022, there was not any material complaint about product quality. Yulon Motor will continue to adhere to the highest-level production standards and proceduresin production processes ensuring the high quality of vehicles and the fulfillment of laws and market standards.
Integration Quality Management System (IQM)
In order to put quality management into practice and initiate vehicle production resumes, Yulon Motor’s Sanyi plant started to develop the Integration Quality Management System (IQM) in 2010, and officially introduced it in 2012. This system covers processes from sourcing from suppliers, assembly, to vehicle evaluation system (VES). In 2021, this system was extended to the production line of new energy business and effectively improved the equipment efficiency, quality yield and energy efficiency. In the future, we will further introduce the artificial intelligence application and, via big data analysis and cloud computation platform, make the best decision driven by real data, so as to achieve the goals of smart manufacturing and corporate digital transition.
Characteristics of the IQM system – checkpoints by processes and quality control process with multiple nodes:
Overview of the IQM system
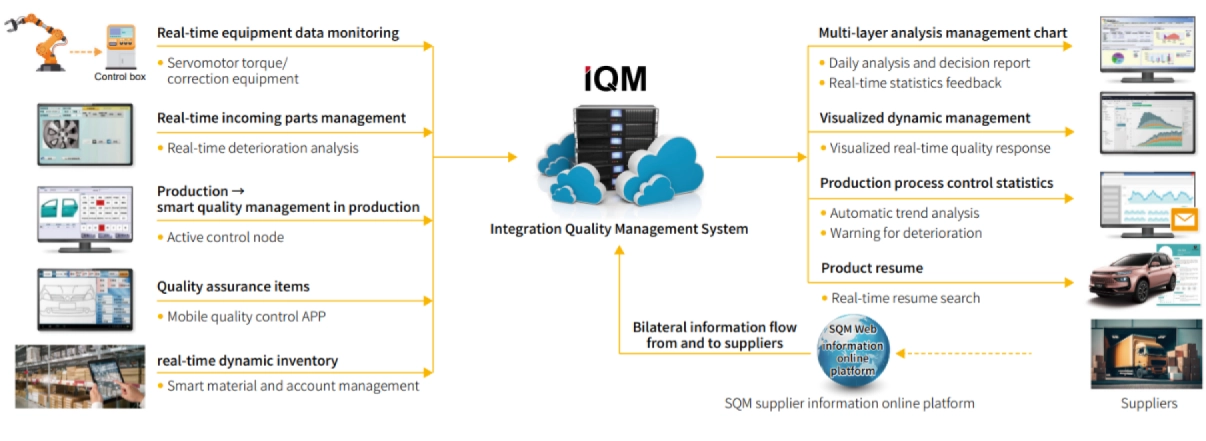
The IQM system built in at the four major work areas: bodywork, painting, engine and accessory, makes sure 100% inspection rate for all quality check items via 180 PADs and 30 PCs that dynamically manage 251 quality control checkpoints in real time while the GO/NO GO quality check stations are adopted in the production process. Visualization of inspection image specifies defective points; the SPC real-time analysis can send early warnings; the billboards can tell the real-time quality feedback and generate analysis and decision reports.
6 major features of the IQM system
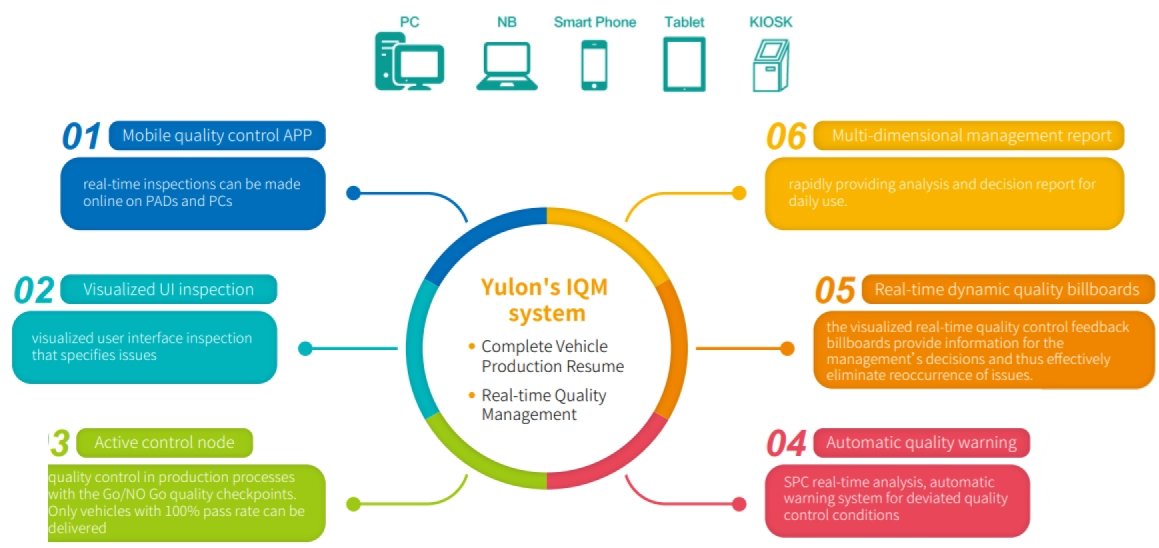
Major product testing system
裕In addition to rigorous vehicle manufacturing processes, Yulon Motor also confirms the stability of all vehicle functions through a series of tests after the vehicle assembly:
Major product testing system
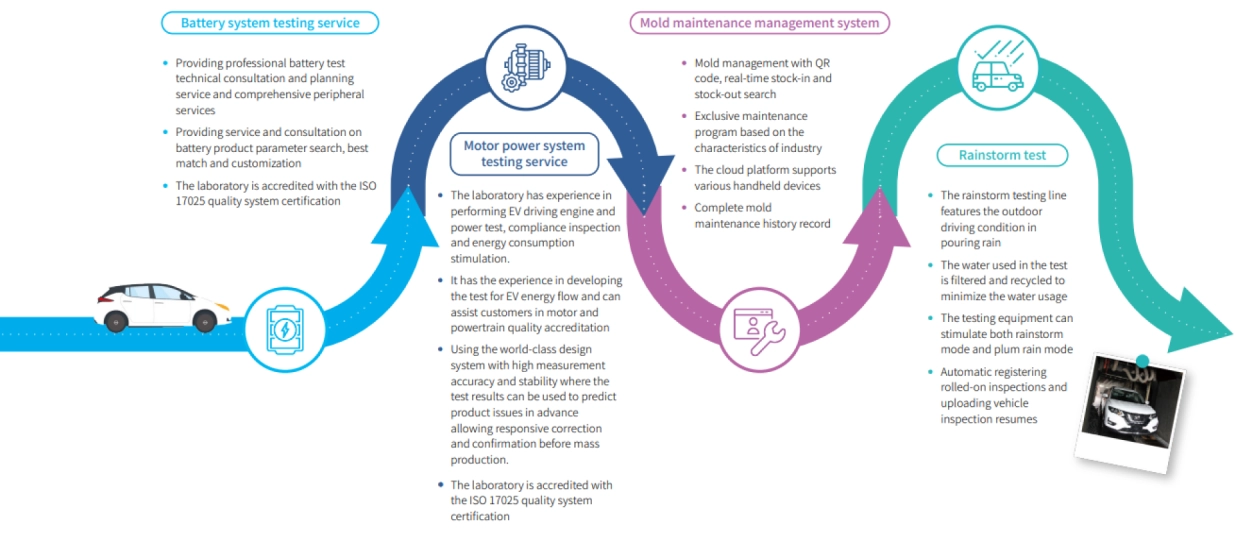
All our vehicles have been tested by the commissioned testing organizations recognized by the central competent authority pursuant to the“ Fuel Economy Standards and Regulations on Vehicle Inspection and Administration.” We have also applied to the competent authority for vehicle energ
Quality management training
In addition to the introduction of quality management system, Yulon Motor also pays attention to the training of relevant personnel to make sure all employees can operate the system effectively and jointly maintain the quality of production lines. In 2022, we held a total of 7 related courses with a total training time of 84 hours and a total of 122 participants.
-
Quality management training courses
-
Product Safety Management
In order to enhance and improve product safety, Yulon Motor’s real-time quantitative quality monitoring system for dynamic road tests can precisely monitor the dynamic road tests. The determination that used to be made by human is now made by the computer with these quantified parameters. The monitoring system then automatically inspect such a determination and data record to improve vehicle inspection quality and preciseness of driving. The captured data and design parameters in the system can later be used in relevant design and by production units for continuous improvement of dynamic driving safety and functionality of vehicles, hence the safer and more trustworthy mobility experience of customers.
-
Road test
-
Dynamic road test monitoring system